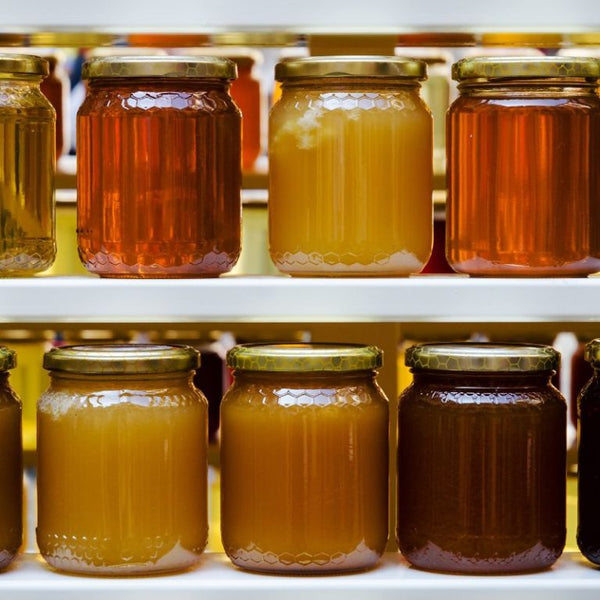
CANNABIS HYDROCARBON EXTRACTION: Hydrocarbon to Biomass ratios
Hydrocarbon to Biomass ratios
One of the commonly overlooked questions when preparing to extract cannabis is how much solvent you will need as well as how much you will lose/consume in the process. Most extraction machines advertise as a closed loop system (CLS) that will recover 99.99% of solvent during processing. This statement is, well, misleading as it is only half true. It is accurate that the collection vessel of the CLS will/should recover the 99.99% of solvent present in that collection vessel. But what about the material columns, are they 99.99% recovered as well? The answer is no, the biomass in your material column will retain a small percentage of the solvent used. Depending on the CLS manufacturer, the specified amounts of solvent needed to extract cannabis vary by a fair margin. The main question is how much solvent you will need for the biomass in the material column to have a successful extraction. We will cover this as well as contact time (the soaking of the biomass), times required, and why it is beneficial. Overall, the general purpose of this article is to give you a base understanding of how much solvent you will need to operate, as well as how much you will consume in the process of cannabis extraction.
Butane
This section will be in reference to both n-butane(R600) as well as isobutane(R600A). This is a general guideline to how much solvent you should expect to use/consume during routine extraction on a CLS. To start, having a refrigerant scale to weigh your solvent injection is incredibly helpful. If you need a C1D1 refrigerant scale, I have used Arlyn Scales out of Rockaway, NY and can speak for their quality and durability. Best practice, if possible, is to place your solvent/injection tank/pressure vessel on to the scale to be able to weigh what you are taking out of it during use. It can also be helpful to employ the scale to weigh what you recover back from your collection vessel. This can be extremely useful if your pressure vessel/solvent tank does not have a sight .
Now that we have a scale to weigh what we use, let’s create reference to the second half of this equation. For this example, let’s say we have a five-pound material/biomass column that we are going to extract the cannabis resin/oils from. The five pounds of biomass requires a minimum ratio of 5:1, butane to biomass to effectively extract the resin/oils. Therefore, the minimum amount of butane you should expect to use for this run is 25 pounds. This is a starting point to gauge your biomass; if you see a low yield of resin/oil from the biomass (sub 7%), then odds are running more butane through the biomass will not yield better results. If we see a nominal yield (8-13%) of resin/oils, then it would be a plausible conversation to use more solvent as there could be more yield to be had from the biomass.
In my personal work, I typically reserve the time spent using extra solvent for biomass that is yielding 14%+ yield of resin/oils. One main reason being, as I stated, time. If you use extra solvent you will need to allow extra time to recover it back to your pressure vessel/solvent tank, and you want to ensure the time spent is worth it. Additionally if you have a desirable yield (14+%), the color, aroma, and consistency of the resin/oil is typically very desirable as well. While strains that have a lower yield can have amazing colors, aromas, and consistencies, it is typically observed that the lower yielding biomass is due to not only the way it was grown but also harvested and stored. Genetics can also play a major role in this, however, that is a lengthy conversation. To put it simply, nine times out of ten the better the genetics the better the outcome will be. If a specific strain of biomass continuously yields a low percentage of resin/oils from a known garden that has other strains of biomass yielding good numbers, then that specific strain may not be the best to grow for extraction. With each strain of cannabis being genetically different, the way the plant grows and produces its resinous glands, known as trichomes, varies heavily. Again, to put things simply, some strains of cannabis are just more viable for extraction than others. An easy way to navigate this is to inspect the biomass before extracting. A simple look with a jeweler’s loop to inspect the trichomes will give you a good idea of what you should expect to see. If you have quality biomass you can expect quality resin/oils, or as they say in the cannabis industry, fire in fire out.
All in all, a great portion of the art of extraction comes through observation. If you feel like a specific biomass has more yield to give, by all means run a higher ratio of butane to biomass! Some extractors will run up to a 10:1 ratio to ensure ALL the resin/oils have been extracted. For most CLS, running 10:1 is time consuming, and the supporting ancillary equipment used to condense the butane struggles to keep up. If you do play with the ratios make sure you take notes, this will be the information you need to justify the use of your time. This information will also benefit you when the time comes to upgrade your equipment, as bigger material columns will inevitably need bigger collection and recovery vessels. Make sure you have plenty of room for solvent!!
Another commonly used ratio is 6:1, butane to biomass. This ratio is commonly used when extractors feel the need to place a chromatographic filter in their CLS to improve quality of resin/oils. In the cannabis industry, this practice has been coined with the acronym CRC, translating directly to Color Remediation Column/Cartridge. There are a few reasons for using slightly more butane in this scenario, the main one being the absorption of butane by the media used for the CRC. Depending on what media is used and how much butane is lost to the absorption varies heavily. This value is typically found using your scale during recovery, as most CRC setups are entirely different from one to another. Additionally, the use of CRC will generally slow the operational speed of the CLS as the media used for CRC needs resonance/contact time with the butane solution to form bonds and remove targeted compounds. Having a little extra butane helps ensure there is minimal resin/oils “stuck” in the CRC that potentially wasn’t soluble enough to make it through the filter.
With a loss of butane due to the absorption by the CRC, you can surely bet you will lose a generous amount of butane to the five pounds of biomass we extracted, as it has also absorbed butane during the extraction process. What’s in question though is how much butane has been absorbed by biomass during processing. If you are processing a dry/cured biomass, the average loss of butane translates directly to a pound for a pound, 1:1. This is on a typical, non-jacketed extraction column. If you have a jacketed column and are holding temperatures below the solvents boiling point, the butane will be further encouraged to stay in the biomass column. This could lead to higher saturation of the biomass and even more loss of butane.
If you lose more butane using a jacketed material column, why would you want to do that? The main reason this would be a plausible scenario in your lab is if you are consistently running frozen biomass, commonly known as fresh frozen. The name comes from the fresh harvest of biomass being immediately frozen, instead of being hung to dry/cure. Frozen biomass will contain up to 70-80% water depending on the cultivar/strain, which does not mix with cannabis extracts/oils. To efficiently extract fresh frozen, the biomass must remain frozen through the extraction process to not allow water to pass on with the resin/oils. Being that the biomass is ~70% water, and butane and water are miscible with one another, the amount of butane lost during fresh frozen runs can vary heavily based on the individual lab, the CLS SOP, and the present operating conditions. Observed butane loss for extracting fresh frozen material, through personal endeavors, is roughly the same as the dry/cured biomass ratio of 1:1. However, if dry/cured biomass is extracted using a jacketed column, expect this ratio to be a good bit higher.
To round this out, we will go over resonance/saturation/contact time of the butane to the biomass. It is common practice to “soak” your material/biomass column to assist with extracting the resin/oils. General time for “soaking” a column is ten minutes. Some extractors feel the need to soak the material for 20 minutes as it helps ensure you extract all the viable resin/oils present. Others feel that 10 minutes is too long to wait, so they go with a five-minute soak or maybe no soak at all. This all depends on how you best see fit to run the strain/biomass at hand, and this is where your notes really start coming in handy. This number can also vary depending on the conditions of the CLS and the supporting ancillary equipment. A simple CLS condition or addition to the process could be the use of CRC. The use of CRC typically negates the need to soak the material column as the extraction process will naturally take longer because the solution will be suspended while it work its way through the CRC filter. This process, unless using granular media, typically adds 5-15 minutes of time to your extraction process. However, this varies heavily based on what CRC media is used and the column size/depth to which it is packed.
From a personal point of view on how much butane to use, work with the tool of observation on your side. If you observe resin/oil at the base of your material/biomass column when emptying or repacking it, that is a clear indication resin/oil was left behind. The material column is for biomass material, not resin/oil collection, so make sure you use enough solvent to thoroughly “flush” it all through. If an increased ratio didn’t help, perhaps a longer soak will, or maybe both. You won’t know until you give it a try and notate your observations. The answer to the perfect amount of butane to use will be in your ability to observe your working environment through trial and error, and of course taking notes.
Propane
Propane slightly differs from butane as it is a shorter chain hydrocarbon. Due to this shorter molecular chain, we need to use more of it to achieve the same result or yield. The typical solvent to biomass ratio used when extracting with propane is 10:1, propane to biomass. Being that the ratio is double that of the amount of butane typically used, you will need a CLS built with proper capacity to accommodate propane to achieve maximum efficiency.
The same general principles from butane apply with propane, with the major difference being you simply need to use more of it! There are two different extraction methods I have personally observed when using propane. One is similar to that of how you would process with butane, complete a 10:1 extraction, recover all the propane to leave you with your extracted resin/oils. Another method involves breaking the 10:1 extraction up into two parts of 5:1 each. The first 5:1 collection will primarily contain the more easily extracted oils known as terpenes. Terpenes are responsible for the smell, taste, and color of the extract. Additionally, they are also the liquid element that is extracted from the biomass.
The Second 5:1 collection will contain primarily the THC and CB compounds of the biomass. These compounds are solid in their natural form, hence being slightly more difficult for the short chain hydrocarbon propane to extract. The best way to accomplish this is to operate a normal 5:1 extraction with no soak of the material, followed by having your material column soaking the with the second 5:1 extraction while the first one is being recovered. This allows an extended period for the material to soak, and also encourages maximum yield from the biomass.
By breaking up your extraction into two separate collections, you can navigate post processing procedures easier by having the majority of the liquids and solids of your extracted resin/oils separated. To clarify, the terpenes and THC/CB compounds will not be completely separated from each other between collection 1 and 2, but this method is a great way to get a head start on things! For one, this allows for easier purging of butane from both the terpenes and the THC/CB compounds, as their purging process is vastly different.
LPG Blends
To bring us full circle, we will discuss the blending of the three hydrocarbons. Many different gas suppliers have started offering premixed hydrocarbon solutions such as: 50/25/25; 50% n-butane, 25% propane, 25% isobutane. The tri-blend of hydrocarbons I just listed has become a standard offering, as it offers the best of what each individual hydrocarbon has to offer the quick recovery of the propane and isobutane coupled with the long chain hydrocarbon n-butane. Some labs prefer to have a cylinder of each hydrocarbon on hand to make their own blends as they fill their pressure vessels. The reason being is the tri-blend might be preferred for dry biomass extraction while a 70/30 mixture of isobutane (70%) and propane (30%) is preferred for fresh frozen extraction.
These numbers can all vary based on what you as the operator/extractor see fit I have simply listed some of the more commonly used percentages for you to start with. If you use more than 30% propane in your blend, ensure that you have a closed loop system that is rated to handle propane. Generally, the certified PSI amount a CLS must have to run propane is 350 PSI, and butane CLS is generally certified at 150 PSI. Even though these systems are built to safely operate under these pressure amounts, if operating correctly, you should never see your system have this much pressure. In my personal time of operating many CLS’s, a pressure over 60 PSI would be a concern, and anything over 100 PSI would be a problem. Whether it be too much propane in the gas mixture or a clogged screen in the CLS, this would merit the suspension of extracting more biomass after the current run is completed and all hydrocarbons in the system have been recovered. Sometimes this process takes an extended period of time if you are navigating a clog or pressure issues. During an extraction with pressure related issues present, please ensure all pressure has been released from all possible valves before taking the CLS apart, as you can never be too sure!! Only when you have identified the pressure causing issue and have found a resolution should you continue to operate your CLS. One of the main causes of pressure related issues in a CLS (besides a clog) is the ancillary equipment failing to accommodate the condensation of the hydrocarbons you are evaporating during processing. To put this simply, if you are evaporating your hydrocarbons faster than you can condense them, your CLS will build pressure. Once your CLS starts building pressure, the process will slow considerably. As stated above, anything over 60 PSI is reason for concern. Typically, I personally like to see the CLS pressures between 5-35 PSI at any given point during the extraction process pending an unusual circumstance, such as CRC or R&D.
When switching between hydrocarbon blends, I always recommend a complete evacuation/disposal of the “blended” hydrocarbons before refilling your pressure vessel. This is because it can become quite confusing to calculate exactly what percentage you have of what hydrocarbon after a few days extracting with the same gas mixture. All in all, use your observations to your advantage and make changes to your process as you deem necessary. Some mixtures/blends of gas work better for some material than others, whether this be an increased yield, color, or quality of resin/oil. Trial and error in cannabis extraction is inevitable, however, with proper notes taken, trial and error occurrences can be minimalized and capitalized on due to the available information at hand.
In general, my personal choice of hydrocarbon for dry or cured material would be 100% isobutane. Evaporation rate of isobutane is much quicker than that of n-butane so I may get more work accomplished in the same given time frame. For fresh frozen extraction, I personally prefer a 50% isobutane, 25% n-butane, 25% propane tri-blend. The rapid evaporation of this blend minimizes the time between each extraction as well as leaving the extracted solution with the slow evaporating hydrocarbon n-butane intact. This allows a wide window for crystallization of the “solution for diamonds and sauce”. This process is typically difficult to achieve with isobutane or propane due to their lower boiling points.
Conclusion
To conclude this article, I would like to mention that many of your local hydrocarbon or “gas” suppliers will have good input as to what other people are ordering for their extractions. Different climates throughout the United States require cultivations or grows to use many different , fungicides, and pesticides unfortunately. Cultivation to cultivation, the nutrients used are generally different as well, affecting how the plant produces terpenes and trichomes. These variations of the grow cycle drastically affect how the resin/terpenes/oil produce and mature on the plant. When extracted, this affects everything from color and clarity, to the taste, smell, and stability of the resin/oil. Knowing the drastic effect that growing products can have on the resin/oils of cannabis from region to region, it never hurts to ask around and see what others are using to navigate the regional challenges. I find this to be a time and opportunity to make new acquaintances in a generally new world of cannabis extraction and cultivation.
Post a Comment!